Automation keeps everything moving. In factories, labs, and cleanrooms, speed and precision are more important than ever. If you’re working with systems that demand tight tolerances, there’s little room for error.
Precision linear stages solve this problem. These motion devices help you achieve accurate, controlled movement across a straight path, and they’re key to boosting productivity in automated environments.
Let’s break down what makes them valuable and how you can use them to strengthen your automation systems.
Contents
What Are Precision Linear Stages?
Precision linear stages are platforms that move parts or tools along a straight path with a high level of accuracy. They typically include a base, a moving surface, and a mechanism that drives the motion. Some use rotating screws to move the platform, while others use magnetic motors for smoother and quieter movement. Built-in sensors help monitor position and keep everything on track.
You’ll find linear stages in simple, one-direction setups or more complex systems that move in multiple directions. Whether you’re aligning a laser, adjusting a camera, or positioning a delicate component, these tools offer tight control over each move.
Companies that specialize in high-accuracy motion control equipment build precision linear stages to meet tight performance standards across a wide range of applications.
Why Precision Matters in Automation
In any automated system, even a tiny misstep can lead to costly problems. A misplaced part, a scratched surface, or a failed product test can throw off an entire process. Precision helps eliminate those issues by ensuring repeatable positioning. When every move is consistent, there’s no guesswork and far less waste.
This level of control is especially critical in fields like electronics, aerospace, and pharmaceuticals, where every detail matters. When your system can place parts with extreme accuracy, you can produce better results faster and with fewer setbacks.
Key Benefits for Automated Systems
Precision linear stages do more than just move things. They deliver real advantages that improve the entire operation:
- Faster cycle times: Movement is quick and direct, with no unnecessary delays. That means more output without sacrificing quality.
- Greater consistency: Every product or task follows the same path. There’s no need for constant recalibration or manual adjustments.
- Reduced downtime: High-precision systems tend to be more durable and avoid issues caused by friction, vibration, or misalignment.
- Long-term cost savings: With less waste, fewer defects, and lower energy use, the savings add up, especially in high-volume environments.
If you’re aiming to reduce errors, improve output, and keep your system running smoothly, precision linear stages can help deliver those results.
Use Cases That Prove Their Value
Precision linear stages are used in several industries:
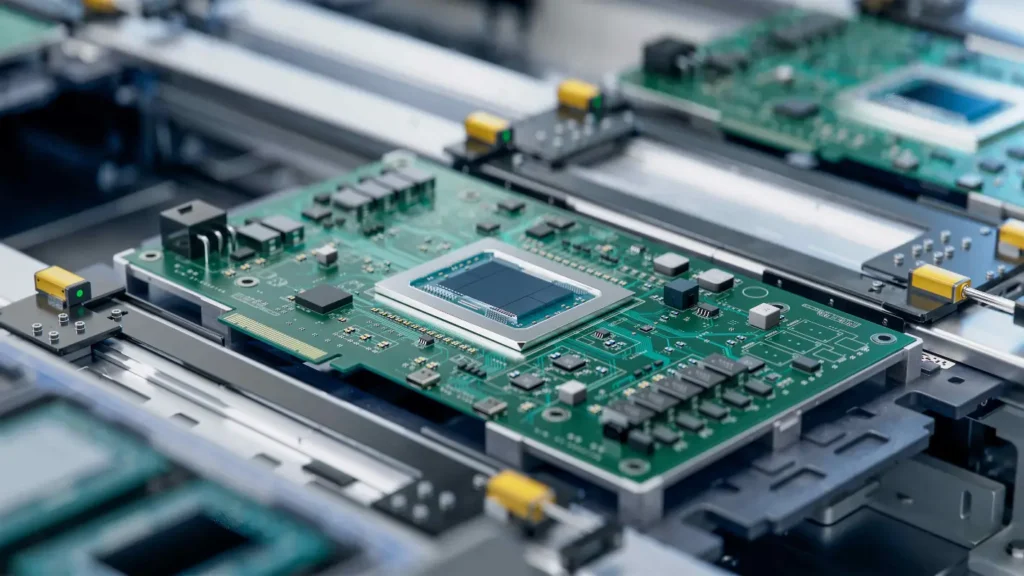
- Semiconductor manufacturing: They move silicon wafers into exact positions during photolithography or etching. Even a tiny misalignment can ruin the entire process.
- Laser cutting and engraving: These stages guide the laser beam with pinpoint accuracy, whether you’re creating micro-circuits or etching detailed patterns on glass or metal.
- Life sciences and medical diagnostics: In lab equipment, they help position slides or samples precisely for testing or imaging. Some are cleanroom-ready to avoid contamination.
- Automated inspection systems: They help sensors or cameras scan items in 3D. The data is only reliable when the underlying motion is stable and exact.
Across industries, precision linear stages prove their value through reliable, accurate motion.
Choosing the Right Stage for Your Needs
Not every application requires the same type of linear stage. Choosing the right one depends on what your system needs to do.
If you need fast, contact-free movement, a motor-driven model might be the best fit. For jobs that require holding steady under heavy loads, a screw-driven version could be more effective.
It’s important to consider how much weight the stage needs to move and how far it needs to travel. Some models are built for small adjustments, while others handle long or complex movements.
Also, think about how the stage will know where it is. Some use optical sensors, while others rely on magnetic or electronic feedback. Each has trade-offs in speed and accuracy.
Finally, match the stage to your environment. Some are built for cleanrooms or labs, while others are sealed to handle dust, heat, or other harsh conditions.
How They Integrate With Modern Automation
What makes them even more valuable is how easily they fit into today’s smart automation platforms.
They can connect with robots, conveyor systems, and cameras. Many are compatible with motion controllers and can be configured into multi-axis setups. Some even offer plug-and-play connections to make installation easier.
More advanced models also support features like data tracking, remote monitoring, and predictive maintenance. These capabilities make them a strong fit for smart factories and Industry 4.0 systems.
Software integration is simple as well. Many stages support common programming languages, making them easy for teams to adapt to existing systems without writing custom code from scratch.
Final Thoughts
When it comes to automation, precise motion is essential. You can’t build high-quality systems without reliable, accurate positioning. That’s exactly what precision linear stages provide.
By keeping alignment tight and movement consistent, they help your processes run smoothly and your outputs meet exacting standards. If you’re looking to speed up production, reduce waste, and gain better control, investing in the right stage can deliver a noticeable and lasting impact.